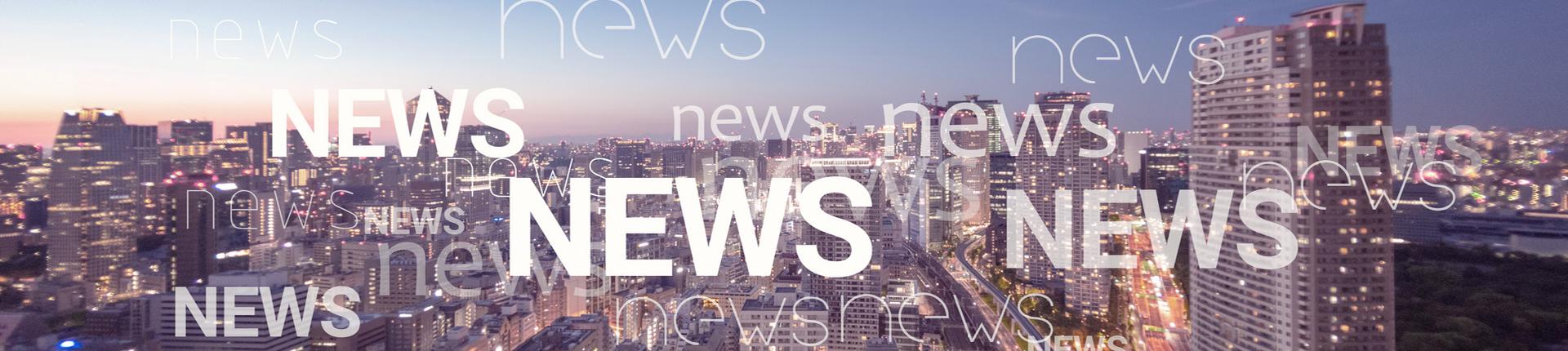
New mode of intelligent service, PLC remote operation and maintenance solution
In industries such as industrial automation, automotive electronics, and transportation, PLC is often a very important device. It is an electronic system for digital operations designed specifically for applications in an industrial environment. PLC technology originated in the United States in the 1960s. It was first to replace mechanical switch devices, and then PLC functions gradually replaced relay control boards and other functions.
The following figure is a common PLC automatic breeding control system. The PC upper computer software develops control logic and communicates with the PLC integrated computer through RS232/network. To realize the functions of automatic feeding, automatic feeding, starting water pump injection, and automatic cleaning operations. It constitutes the entire control system of automatic breeding.
In the traditional sense, PLC is only used for process control in various industries, for closed-loop control of temperature, pressure, flow, motor, and other parameters. In some scenarios, a touch screen is inserted in the communication port to monitor or control the real-time data of the PLC.
With the advent of the "Industry 4.0" era, data has become an important resource in this era. Products not only need to realize the closed-loop control of the system, but also should know whether the system is running smoothly, the impact of application scenarios on equipment, and more information. Need feedback from the data. Whether it is the industrial Internet of Things or smart factories, the demand for this kind of networked and data-based applications is increasing.
How to realize data and intelligent management of equipment?
The first step is to be able to complete the production process based on automation.
The second step is to realize real-time data reporting. Push the running status data of the device to the cloud in real time for big data analysis. Collect the operation status of the equipment, and realize the remote monitoring, early warning, and operation, and maintenance of the equipment.
One way to make the smart gateway in the above figure
The gateway reports the device data in the field to the cloud server. The advantage of this method is that it can centrally control multiple PLCs of different brands, and push the on-site operating conditions of terminal devices, including device switch status, device ID, and main system parameters to the cloud. Users can use WEB on computers, tablets, and mobile phones. The browser accesses the cloud and observes the status of the equipment on the PLC.
Another way is to combine IoT technology with PLC technology
Make a remote-function PLC device and establish a connection with the cloud platform by means of 4G, WiFi, Ethernet, etc. Through the cloud system to achieve equipment failure detection function, remote maintenance regular reminders, remote monitoring of equipment operation reports, it is possible for equipment manufacturers to remotely control equipment operation status and improve equipment management efficiency.
For equipment manufacturers, equipment sales are only the first step, and then they will face equipment debugging and maintenance. In the past, once equipment problems occurred, manufacturers would send maintenance engineers to the site for inspection and repair. With the increase in personnel costs nowadays, how to implement remote debugging and maintenance of equipment with limited manpower is a big problem.
With the development of the Internet of Things technology, more and more companies hope to be able to remotely diagnose and maintain equipment, to monitor and record the status and faults of the equipment system in each area in real-time, and to prompt faults in advance to ensure that the entire after-sales, Maintain data recording, query, and analysis, and achieve the requirements for remote management of equipment.
A low-cost, high-performance MCU implementation of the ARM architecture is recommended here. It can be used as a gateway product alone, and it is compact and can be embedded in general equipment.
The FET1061-S core board is a high-performance MCU designed by Forlinx Company based on NXP's I. MX RT1061 cross-border processor, equipped with an ARM Cortex-M7 core, running at 528MHz, 1MB on-chip SRAM, and 4MB of ROM. The size is only 30×30×3mm, it adopts stamp hole packaging design, industrial-grade design, and the operating temperature is -40℃~+85℃, which is convenient for embedding in the equipment of various sizes.
In order to make it easier for customers to evaluate and use, the OK1061-S development board leads to UART, Ethernet*2, USB, CAN, CAN FD, HS_GPIO, PWM, ADC, and other rich peripheral functions, and supports real-time systems such as bare metal and FreeRTOS. Support OTA upgrade can run RT-Thread, AliOS, LiteOS, and other domestic Internet of Things operating systems.